Specification Technologist - Coventry, United Kingdom - Handmade Speciality Products Ltd.
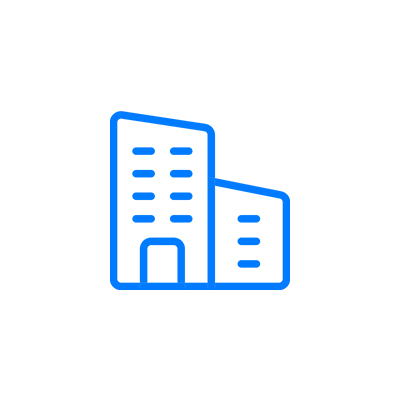
3 weeks ago
Description
Handmade Speciality Products is a family-owned bakery manufacturer, operating out of a BRC A grade production facility in Coventry.From humble beginnings making a small range of flapjacks in a kitchen in 1987, our company soon became the market leader in single serve flapjacks, muffins, biscuits and cake slices.
Today, Handmade specialises in supplying both private label and in-house branded ranges across the UK and Europe. We have customers in both the retail and foodservice sectors, including national retail chains, wholesalers and independents. Our forward-thinking team are passionate about our products and customers, focused on being great innovators through NPD.The company is continuing to grow with ambitious plans to better our offering and service, supported by a very experienced senior team with long bakery backgrounds.
Being privately owned the company benefits from continual investment in both our factory and people.The Specification Technologist function at Handmade is to provide advice relating to scientific, technical and legislative issues. Their key responsibility is to help the site understand current food safety laws and packaging requirements. This includes ensuring products are safe for consumption and correctly labelled to meet legal requirements. Correct labelling requires precise information about allergen and nutritional content, warning messages, and artwork that is appropriate.
The Specification Technologist will work very closely with the Quality Manager and make sure the products being produced are ready for sale and there are no legal issues preventing the product from reaching the market.
They are also required to support the Technical Manager and deputies in the absence of the Quality Manager ensuring the company operates to the highest quality and food safety standards and to continuously monitor and improve the quality and safety of products in collaboration with all department managers.
Key responsibilities:
- Creating and reviewing product specification requirements. They must create simple product specifications, which can be understood by production staff and managers. Review and maintain Customer Specifications Manuals of signed Specifications.
- Review and approve packaging details and product artwork. The Technical Coordinator will be closely involved in the process of designing labels and packaging. They must ensure that all legislative requirements are met while keeping the product development team happy with the design of the product.
- Create standard operating procedures for artwork creation. They will develop operating procedures which highlight the content that must be included in every piece of artwork or promotional material created by the company. The artwork that is being created must be appropriate for every market that the facility's products are being sold in.
- Have a very highlevel awareness of labelling requirements. The Technical Coordinator must have a strong understanding of the regulatory requirements for labels. They must understand the legislative requirements for every market in which the business sells products. They must transfer this knowledge to other staff in the bakery in an easytounderstand way. They must be on top of labelling policies, food safety legislation, and any upcoming changes.
- Manage specifications projects and deliver them on time. They will have to oversee a variety of projects relating to product specifications. These projects must be prioritised and completed in a timely fashion.
- Be available to answer questions from colleagues, visitors and auditors. Colleagues and auditors will occasionally have questions about how a product should be packaged, evaluated, or presented. They may also have questions about food standards or correctly evaluating product quality. The Technical Coordinator must be able to accurately answer these questions in an easytounderstand way.
- Provide advice on technical aspects of products. The Technical Coordinator must evaluate the products being produced, providing advice on their shelf life and nutritional value.
- Help bring new products and promotional products to market. The Technical Coordinator works closely with the product development team to ensure new product lines and promotional products have fulfilled the requirements necessary to go to market.
- Compiles technical reports, produces accurate statistics, relevant figures, undertakes data analysis, identifies and investigates variations.
- Develops and maintains technical databases and spreadsheets.
- Reports any breaches of safety procedures to supervision/management.
- Actively participates in and promotes company health and safety campaigns, policies and procedures, and ensures personal safety and that of colleagues at all times.
Job Types:
Full-time, Permanent
Benefits:
- Onsite parking
Schedule:
- Monday to F
More jobs from Handmade Speciality Products Ltd.
-
Technical Assistant
Coventry, United Kingdom - 1 day ago