Head of Quality - Chippenham, United Kingdom - Dymag Group Limited
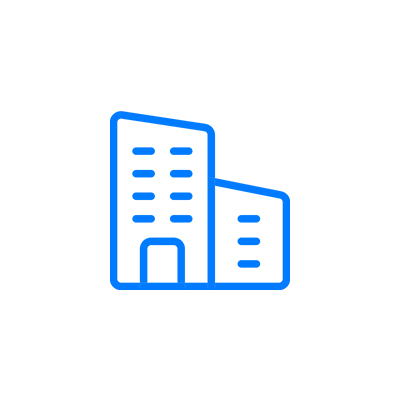
3 weeks ago
Description
With a history spanning over four decades, Dymag is an iconic designer and manufacturer of motorsport wheels.We have a rich heritage in Formula One, IndyCar, Moto GP, Isle of Man TT, as well as projects for supercar and superbike manufacturers - including a new world speed record for the fastest production car in late 2020.
We're now at a critical stage in our long history. With huge demand for our products internationally and new partnerships, we're significantly scaling up production and growing our team. This is where you come in...
As Head of Quality, you will be responsible for maintaining quality compliance and driving product and process improvements through continuous improvement initiatives.
You will analyse current practices, define new processes and collaborate with teams across the business to implement and embed changes in workflows, systems and procedures.
You will also have oversight of our facilities management in our existing premises, and in any new sites (including potential new sites abroad).
This is a hands-on role in which you will have the autonomy to drive change and shape new business processes, from carrying out root cause analysis through to developing and directly implementing engineering solutions.
You will also ensure that quality is embedded in the planning and execution of strategically significant projects, working with customers in the UK and abroad.
Your main duties willQuality & Continuous Improvement
- Design and develop quality targets and dashboard metrics to help the growth, efficiency and profitability of the business.
- Audit current manufacturing and business processes, as well as supporting team members to develop new processes and define best practice standards.
- Proactively identify areas for improvement through observation of core processes, audit results, customer feedback and analysis of performance and quality metrics, and work with team members collaboratively to develop potential solutions.
- Prepare a plan/cost benefit analysis, setting priorities and resources required to achieve identified improvement projects.
- Ensure improvement objectives, milestones and measures are established for each improvement project and take the lead in implementing solutions to ensure expected benefits are achieved within the agreed timescales.
- Lead CPAR process and take responsibility for fault resolution as appropriate, including taking a handson role in fixing problems.
- Develop reports for senior management on quality and continuous activities including accomplishments, projected activities and recommendations for change within the business.
- Communicate key lessons learned and best practices from improvement projects.
- Support team leaders in rolling out new processes and best practice, such as through delivering training and providing updated documentation.
- Actively promote continuous improvement behaviours to all employees.
- Staying uptodate with developments in management and process optimisation.
- Support the achievement of external quality standards (e.g. ISO) ensuring that all activities are embedded to ensure compliance and by supporting all regulatory audits and closure of any findings
- Support project development, including process FMEA, control plan, quality instructions, checking fixture designs, process capabilities and inputting into feasibility signoff of mechanical drawings before release.
- Work closely with the engineering team to ensure that quality is designedin, including advanced quality planning and appropriate dimensioning, tolerancing, measurement plans and control plans.
Customer Liaison
- Contributing to OEM projects, including agreeing and monitoring quality standards prior to and during development and manufacture.
- Occasional local and international travel to customers to clarify technical requirements with customers on new projects and discuss customer concerns, or to support Supply Chain & Procurement Manager with the selection and management of suppliers by carrying out supplier audits.
- Act as customer interface for audit issues and develop response and corrective actions, including leading all warranty and service problem solving activities and reporting back to OEMs.
Strategic Leadership
- As part of the Senior Management Team, contributing to strategic planning, identifying commercial and operational risks and opportunities and prioritising actions arising.
- Leading on strategically significant projects, including new factory set up in remote locations, ensuring that Business Management Systems are established to ensure consistent quality standards are met.
Team Development
- Line management and professional development of quality and facilities/HSE team members, including conducting regular onetoone reviews and appraisals, recruitment and induction, coaching, performance management and ongoing career development.
- Training production/operations team members on routine daytoday quality
More jobs from Dymag Group Limited
-
Machine Shop Lead
Chippenham, United Kingdom - 1 week ago